Connecting Clean: Understanding Sanitary Flanges in Hygienic Systems
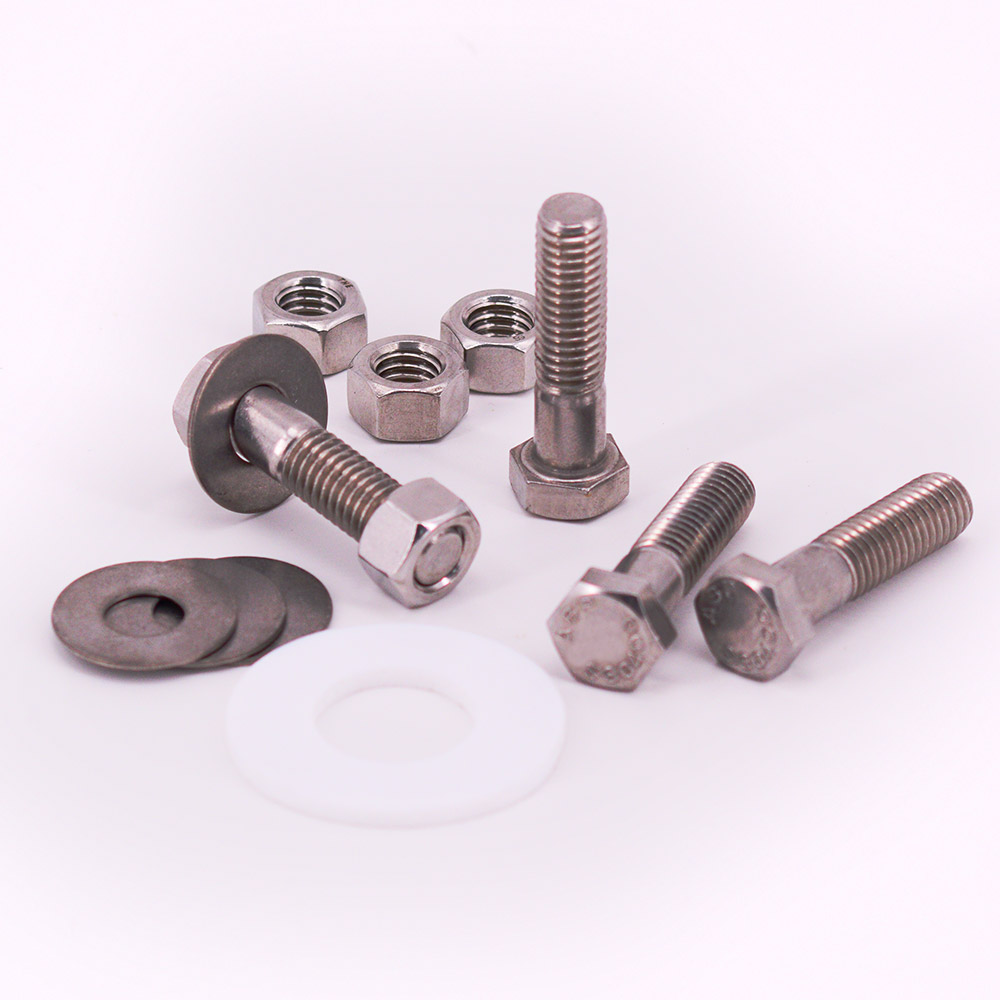
When it comes to building hygienic fluid systems—whether in food processing, pharmaceuticals, or biotech—how you connect things matters as much as what you’re moving. While tubing, pumps, and valves often get all the attention, sanitary flanges play a quiet but crucial role in holding it all together—literally.
What Are Sanitary Flanges?
Sanitary flanges are specialized connectors used to join sections of pipe or tubing in sanitary processing lines. Unlike typical industrial flanges, these are engineered for cleanability, corrosion resistance, and compliance with strict hygiene standards.
They’re often made of 316L stainless steel—a material known for resisting pitting, scaling, and chemical reactions—making them ideal for clean-in-place (CIP) and sterilize-in-place (SIP) operations.
Why Use Sanitary Flanges Instead of Welds or Clamps?
Here’s where things get interesting. While welding might offer a permanent connection and tri-clamp fittings are quick and easy, flanges offer a robust, semi-permanent middle ground. They are ideal for:
- High-pressure systems
- Frequent disassembly and reassembly
- Larger-diameter piping
- Durability in extreme temperatures
Flanged connections also allow for bolt kits to ensure secure and even compression—vital when sealing with gaskets in environments where leaks simply aren’t an option.
Common Types of Sanitary Flanges (And When to Use Them)
- Flange Gasket Bolt Kits
These kits provide all the essentials—gaskets and bolts—needed to create leak-free seals between flanged ends. They’re perfect for quick maintenance or new installations. - Tri-Clamp Flange Adapters
Want the flexibility of tri-clamp systems with the strength of a flange? These adapters bridge the gap. Ideal for hybrid setups. - Tube Slip-On Flanges
Designed to slip over piping and then be welded in place, these offer a balanced mix of strength and simplicity—great for moderate-pressure environments. - Tube Weld Neck Flanges
For critical, high-pressure applications, these flanges offer maximum reinforcement thanks to their neck-like design that allows for gradual stress transfer.
Where They’re Used (Real-World Scenarios)
- In Dairy Plants: For connecting pasteurization systems where consistent pressure and temperature are essential.
- In Biotech Labs: For ensuring sterile pathways during chemical transfer.
- In Beverage Manufacturing: Where frequent equipment teardown is required for flavor-switching production lines.
Don’t Forget the Gasket
A flange without the right gasket is like a door without a seal—technically closed, but not air-tight. Always pair your sanitary flange with the proper FDA-grade gasket material, such as EPDM, Viton, or PTFE, based on your chemical exposure and thermal requirements.
Final Thoughts: The Unsung Backbone of Clean Processing
In the realm of sanitary processing, every detail counts. While often overshadowed by pumps or automation tech, sanitary flanges are foundational to ensuring that a clean system stays clean—even under pressure.
Think of them not just as connectors, but as gatekeepers of hygiene and system integrity. The next time you’re specifying equipment for a cleanroom or production line, give flanges the attention they deserve—they’re doing more work than you think