How to Reduce PCB Assembly Costs Without Sacrificing Quality
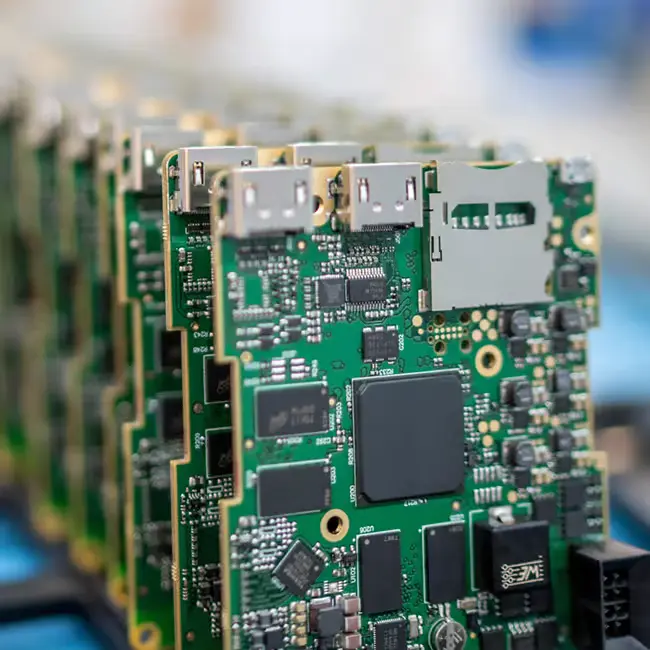
In today’s competitive electronics manufacturing landscape, finding the optimal balance between cost reduction and quality maintenance in PCB assembly is a critical challenge. Companies like RAYMING PCB have demonstrated that implementing strategic cost-saving measures doesn’t have to come at the expense of product reliability or performance. This article explores practical approaches to reducing PCB assembly costs while ensuring the final product meets or exceeds quality standards.
Design for Manufacturability (DFM)Optimize Component Selection and Placement
One of the most effective ways to reduce assembly costs begins at the design stage. Carefully selecting components with standardized footprints and optimizing their placement can significantly impact manufacturing efficiency.
Strategic component choices:
- Use standard components instead of custom ones whenever possible
- Select components that are readily available from multiple suppliers
- Consider components with similar reflow profiles to simplify the soldering process
- Opt for surface-mount technology (SMT) over through-hole components where appropriate
RAYMING PCB’s design engineers often work closely with clients during the early stages to recommend component substitutions that maintain functionality while reducing assembly complexity and cost.
Standardize Design Elements
Standardization across PCB designs can lead to substantial cost savings:
- Maintain consistent pad geometries and spacing
- Use standard board outlines and dimensions when possible
- Establish uniform mounting hole locations
- Create modular designs that can be reused across product lines
Minimize Layer Count
Each additional layer in a PCB increases manufacturing complexity and cost. A thorough design review often reveals opportunities to consolidate routing and reduce layer count without compromising signal integrity or thermal performance.
Panelization Strategies
Properly designed PCB panels can dramatically reduce assembly costs by enabling more efficient use of manufacturing equipment.
Optimize Panel Utilization
Maximum material utilization reduces waste and cuts costs:
- Arrange boards to minimize unused space on the panel
- Consider using irregularly shaped panels that maximize the number of boards per panel
- Design break-away tabs and routing paths that minimize material waste
RAYMING PCB utilizes advanced panelization software to achieve optimal board arrangements, often increasing the number of units per panel by 10-15% compared to standard rectangular panels.
Panel Design Considerations
Effective panel design goes beyond simple arrangement:
- Include appropriate fiducial marks for accurate component placement
- Design tooling holes that align with assembly equipment
- Add test points accessible during panel-level testing
- Incorporate panel-level identifiers for traceability
Component Procurement Strategies Volume Purchasing
Leveraging volume discounts can significantly reduce component costs:
- Consolidate orders across multiple products
- Schedule regular bulk purchases instead of frequent small orders
- Consider partnering with suppliers for long-term pricing agreements
Alternative Sourcing
Identifying alternative component sources provides cost flexibility:
- Qualify multiple suppliers for critical components
- Consider house-branded alternatives to premium components
- Evaluate regional suppliers to reduce shipping costs and lead times
RAYMING PCB maintains relationships with an extensive network of component suppliers, allowing them to source components at competitive prices while ensuring authenticity and quality.
Just-in-Time Inventory
Balancing inventory costs with production needs:
- Implement inventory management systems that reduce carrying costs
- Develop relationships with suppliers who can provide quick-turn deliveries
- Consider consignment arrangements for high-volume components
Assembly Process Optimization Automated Assembly
Maximizing automation reduces labor costs and improves consistency:
- Design for maximum automated assembly compatibility
- Minimize manual soldering requirements
- Consider design modifications that eliminate the need for manual adjustments
RAYMING PCB has invested in state-of-the-art automated assembly equipment that handles both high-volume production runs and small-batch prototypes with equal efficiency.
Line Setup Optimization
Reducing changeover time between production runs:
- Group similar products for consecutive manufacturing
- Standardize programming for pick-and-place machines
- Create reusable assembly profiles for recurring products
Testing Strategies
Optimizing test procedures reduces costs while maintaining quality:
- Implement in-line automated optical inspection (AOI)
- Design for in-circuit testing with minimal fixture complexity
- Develop functional tests that efficiently verify critical parameters
Quality Assurance That Reduces Costs
Contrary to common perception, comprehensive quality assurance can actually reduce overall costs by preventing expensive rework and field failures.
Early Defect Detection
Catching issues early in the process is always more cost-effective:
- Implement consistent incoming inspection for critical components
- Use automated inspection at multiple stages in the assembly process
- Apply statistical process control to identify trends before they cause defects
RAYMING PCB’s multi-stage inspection process identifies potential issues early, reducing rework costs by over 30% compared to end-of-line testing alone.
Process Monitoring and Improvement
Continuous improvement drives long-term cost reduction:
- Monitor key process indicators to identify improvement opportunities
- Implement periodic process audits and improvement initiatives
- Analyze defect data to prioritize improvement efforts
Documentation and Traceability
Proper documentation reduces troubleshooting time and improves process control:
- Maintain detailed assembly records for each production batch
- Implement component traceability systems
- Document process parameters for successful production runs
Strategic PartnershipsManufacturer Collaboration
Early collaboration with PCB assemblers like RAYMING PCB can yield significant cost benefits:
- Involve manufacturing partners during the design phase
- Leverage their expertise in component selection and sourcing
- Align design decisions with their equipment capabilities
Contract Negotiation
Strategic contract structures can align incentives for cost reduction:
- Consider longer-term contracts that allow manufacturers to invest in process improvements
- Implement shared-savings programs for cost reduction initiatives
- Develop realistic quality metrics that balance cost and performance
RAYMING PCB offers collaborative partnership models where cost savings from process improvements are shared with clients, creating a win-win scenario for ongoing cost reduction.
Advanced Technologies for Cost ReductionSelective Soldering
When mixed-technology boards are unavoidable:
- Use selective soldering techniques for through-hole components
- Design wave solder pallets that minimize manual masking
- Group through-hole components to simplify the selective soldering process
Conformal Coating Automation
For assemblies requiring environmental protection:
- Design for automated conformal coating application
- Specify areas requiring protection and masking clearly
- Consider alternative protection methods for moisture-sensitive components
Advanced Placement Technologies
Leveraging cutting-edge assembly equipment:
- Utilize high-speed placement machines for standard components
- Implement precision placement for fine-pitch components
- Consider package-on-package technologies for space-constrained designs
RAYMING PCB continually invests in advanced assembly technologies that increase throughput while maintaining placement accuracy, passing the resulting cost savings to clients.
Case Study: Cost Reduction Success
A recent project at RAYMING PCB demonstrates how these principles work in practice. When a telecommunications client needed to reduce assembly costs for a high-volume product:
- Design review identified opportunities to reduce layer count from 8 to 6 layers
- Component consolidation reduced the unique part count by 18%
- Panelization optimization increased units per panel by 22%
- Automated testing reduced labor costs by 35%
The result was a 28% reduction in overall assembly cost with zero impact on product quality or reliability, demonstrating that strategic cost reduction need not compromise performance.
Conclusion
Reducing PCB assembly costs while maintaining quality requires a multifaceted approach that spans the entire product development cycle. By implementing design for manufacturability principles, optimizing procurement strategies, streamlining assembly processes, and leveraging strategic partnerships with experienced manufacturers like RAYMING PCB, companies can achieve significant cost savings without sacrificing product quality.
The most successful cost reduction initiatives involve collaboration between design teams, component suppliers, and assembly partners, with a focus on total cost of ownership rather than individual line items. By taking this holistic approach, manufacturers can remain competitive in price-sensitive markets while delivering the reliability and performance their customers demand.
Remember that cost reduction is not a one-time event but an ongoing process of continuous improvement. Working with experienced partners like RAYMING PCB, who understand both the technical and commercial aspects of PCB assembly, provides the foundation for sustainable cost optimization that supports long-term business success